Lithography is an essential step in the manufacturing process of semiconductor devices, where geometric patterns are created on a photoresist layer using exposure and development, followed by etching processes to transfer the patterns from the photomask to the substrate.
Since the birth of the first lithography machine in 1961, lithography machines have evolved through the development path of contact → proximity → projection, with step-and-scan lithography machines in the projection category now being the mainstream.
At different stages, each generation of lithography machines has encountered unprecedented challenges and problems, while lithography technology has also continuously evolved in this process.
01
Development Path of Lithography Technology
Contact Lithography Technology
Contact lithography technology emerged in the 1960s and was the main lithography technology during the era of small-scale integrated circuits, characterized by low yield and high cost.Contact lithography technology involves direct contact between the photomask and the photoresist on the wafer surface, exposing the entire substrate at once. The size relationship between the photomask pattern and the wafer pattern is 1:1, and the resolution can reach the sub-micrometer level. Contact lithography can reduce the diffraction effect of light, but the friction between the wafer and the photomask during the contact process is prone to forming scratches and causing particle contamination, which reduces the yield of the wafer and the service life of the photomask. It is necessary to frequently replace the photomask, hence the introduction of proximity lithography technology.
Advertisement
Proximity lithography technology was widely used in the 1970s. In proximity lithography technology, the photomask and the photoresist on the wafer surface do not make direct contact, leaving a gap filled with nitrogen.
The characteristic of proximity lithography technology is that the minimum resolution size is directly proportional to the gap. The smaller the gap, the higher the resolution. The disadvantage is that the spacing between the photomask and the wafer will cause the light to produce diffraction effects, so the spatial resolution limit of the proximity lithography machine is about 2 micrometers. With the reduction of feature size, projection lithography technology emerged.
Projection lithography technology appeared in the mid-to-late 1970s and can effectively improve resolution.
Based on the far-field Fourier optical imaging principle, a projection imaging objective lens with a reduction ratio is used between the photomask and the photoresist. The early photomask to substrate pattern size ratio was 1:1. With the continuous reduction of integrated circuit sizes, step-and-repeat lithography technology with a reduction ratio has emerged.Step-and-Repeat Lithography Technology
Step-and-repeat lithography is mainly applied to processes above 0.25 microns, where the photomask remains stationary during exposure, and the wafer moves step by step to complete the entire exposure process. As the integration of integrated circuits continues to improve and the chip area increases, there is a demand for a larger exposure area in a single exposure, which has driven the emergence of more advanced step-and-scan lithography machines.
Step-and-Scan Lithography Machines
After the process technology developed to 0.25 microns, the scanning exposure field size and exposure uniformity of step-and-scan lithography machines have more advantages, gradually becoming the mainstream lithography equipment (DUV and EUV). It utilizes a 26mm x 8mm slit and adopts a dynamic scanning method (synchronous movement of the photomask and the wafer), which can achieve a 26mm x 33mm exposure field. After the current exposure field scanning is completed, it moves to the next exposure field until the entire wafer is exposed.
Since SVGL introduced the Micrascan I step-and-scan lithography machine in 1990, the lithography machine industry has entered the DUV era. Through multiple exposure and other technical means, DUV has been the market leader until the mass production of 7nm chips.
However, as the process progresses to 5nm, the combination of DUV and multiple exposure technology can no longer meet the mass production requirements, and EUV lithography machines have become a necessity for front-end processes. As the process nodes continue to evolve, the industry's requirements for EUV lithography machines are increasing, and more expectations have been raised for their development prospects and paths.
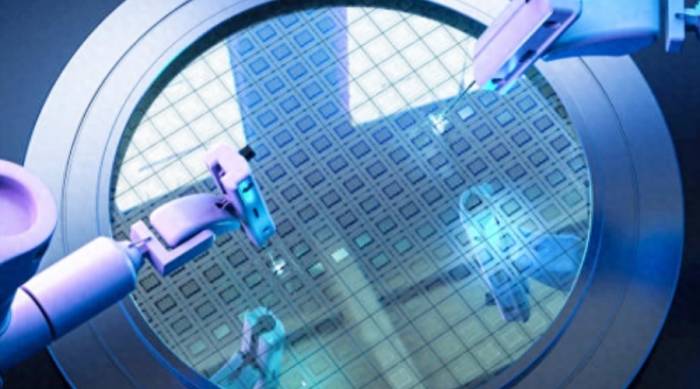
For the future development of lithography technology, the industry is actively seeking high-precision and economical methods to generate patterns on wafers. Several companies/research institutions have announced their research progress, let's take a look at the new options they have brought to lithography technology. 02One of the Choices: High NA EUV Lithography Machines
The light source wavelength used in lithography machines has evolved from the earliest ultraviolet (UV) sources, such as the g-line (wavelength of 436 nm) and i-line (wavelength of 365 nm), to deep ultraviolet (DUV) sources represented by KrF (wavelength of 248 nm) and ArF (wavelength of 193 nm), and now to the extreme ultraviolet (EUV) with a wavelength of 13.5 nm.
With the continuous reduction of the light source wavelength, the resolution of the lithography machine's single exposure has been continuously improved. The most advanced EUV lithography machines currently have an exposure resolution of 13 nanometers, which can be used for the production of 3 nm process chips.
Nowadays, the competition among chip manufacturing companies such as TSMC, Samsung, and Intel has entered the advanced process track. In this process, EUV extreme ultraviolet lithography equipment has also become the focus of contention among various manufacturers.
It is reported that from 2024 to 2025, TSMC will receive 60 EUV lithography machines, with an estimated total cost exceeding 12.2 billion US dollars; Intel took the lead in embracing the world's first High NA EUV lithography machine; Samsung is also eager to try the High NA EUV lithography machine, trying to catch up with TSMC.
However, while pursuing the most advanced lithography machines, there is both joy and pain.
The joy lies in that being the first to get the most advanced lithography machines means that it can greatly improve its chip manufacturing capabilities and efficiency, helping the company to gain a competitive advantage in the future advanced process technology.
The pain lies in the high price of EUV, which makes major chip manufacturers suffer. It is reported that the current price of the 0.33NA EUV lithography machine is about 181 million US dollars per unit, and the new generation of High-NA (0.55NA) EUV has doubled to 292-362 million US dollars per unit. After entering the era of sub-1 nanometer angstrom, ASML plans to launch more advanced Hyper-NA (0.75NA) EUV lithography machine equipment, and its price may exceed 724 million US dollars.
This method is obviously fine enough but not economical enough. Therefore, there are also many institutions in the industry that are exploring the cost reduction of High NA EUV, and they mainly focus on improving the light source resolution.
The laser plasma EUV light source (EUV-LPP) currently used by ASML is expensive and inefficient, with a photoelectric conversion rate of only 3%-5%. To improve power, there are several development paths to choose from: some people use the traditional LPP light source system, on the basis of the existing, continuously increase power; others use the time-sharing high-power fiber laser shooting liquid tin target technology, the light source made by this method, its light source power is expected to exceed the traditional LPP several times.Using a Free-Electron Laser (FEL) scheme with an Energy Recovery Linac (ERL) is also a viable approach. Researchers at the High Energy Accelerator Research Organization (KEK) in Japan believe that harnessing the power of particle accelerators may lead to the acquisition of Extreme Ultraviolet (EUV) light sources that are cheaper, faster, and more efficient.
FEL generates ultra-intense lasers by utilizing the motion of electrons in a magnetic field, with an efficiency twice as high as conventional EUV light sources, and an energy conversion rate exceeding 30%. It also offers advantages such as low cost and high power. In terms of power consumption, FEL light sources are also significantly lower than EUV-LPP light sources. Moreover, EUV-FEL can be upgraded to BEUV-FEL to achieve finer patterning with shorter wavelengths (6.6-6.7 nm). It can also variably control the polarization of FEL light to achieve High Numerical Aperture (NA) lithography.
It is reported that the industry has already designed an FEL light source based on the Energy Recovery Linac (ERL) for future lithography and has researched and developed the main components. The FEL light source has many advantages in terms of EUV power, upgrade to BEUV-FEL, polarization control for High NA lithography, power consumption, and the cost per lithography machine.
The EUV-FEL light source is also considered to be the most promising light source for future lithography.
However, there are still many people in the industry who hold different views on the future development of lithography technology.
03
Option Two: Nanoimprint Lithography (NIL)
The "competition" between nanoimprint and lithography technology has a long history.
Nanoimprint is a micro-nano processing technology based on polymer embossing technology. Nanoimprint requires a template, just like the template on movable type printing engraved with the characters to be printed, the nanoimprint template has the nanostructures to be manufactured, and then by heating and pressing, the nanostructures on the template are replicated into the nanoimprint material.
It can be vividly compared to the movable type printing technique.Compared to photolithography technology, nanoimprint lithography has the following advantages:
Lower cost: Compared to photolithography, the cost of nanoimprint lithography is lower, mainly because the nanoimprint equipment is relatively inexpensive and the process is simple, making it easier for mass production.
Higher precision: By carefully designing and manufacturing high-precision "stamps," nanoimprint lithography can achieve high-precision circuit patterns better than 10nm, providing higher precision assurance for chip manufacturing.
Wider application fields: Nanoimprint lithography is not only suitable for the manufacturing of logic chips and memory chips but can also be widely applied to mass production in fields such as DOE, AR/VR diffractive optical waveguides, biochips, LEDs, etc., and has great market potential.
At present, nanoimprint is widely used in fields such as LEDs, AR, and VR. Nanoimprint has been developed for more than 20 years, but for a long time, it was not widely accepted in the semiconductor field due to the high defect rate and low yield of the products made by nanoimprint, while photolithography technology developed faster and better.
In the past decade, with the optimization of the process and the control precision of nanoimprint lithography, which has reached a new level, nanoimprint, which was once denied by photolithography, has ushered in a high point.
However, nanoimprint lithography also has its shortcomings. It is a physical contact processing technology. During the physical contact process, some external defects are prone to occur. The semiconductor industry has a very low tolerance for defects. Some people in the industry believe that nanoimprint is a very promising technology, while others believe that its defect rate is relatively high and not suitable for semiconductor processing.
After falling behind ASML in the traditional photolithography field, Canon has been looking for new breakthroughs in the direction of semiconductor manufacturing, and one of its key explorations is nanoimprint lithography.
In mid-October last year, Canon announced the launch of the FPA-1200NZ2C nanoimprint semiconductor manufacturing equipment, which can manufacture 5nm chips. According to the CEO of Canon, the equipment price will be "one order of magnitude less than ASML's EUV lithography machine."Ge Haixiong, the founder of Pulin Technology, said at the end of last year: According to the latest reports, Canon's nano-imprint lithography technical indicators have been on par with DUV lithography technology, and some indicators have even reached the lithography technology of EUV.
Regarding the future of nano-imprint technology, Ge Haixiong said that based on the technical parameters and indicators provided by Canon, nano-imprint may create some beneficial supplements for the semiconductor field, as semiconductor lithography equipment from ASML and Nikon has been widely used in production lines, and nano-imprint can be seen as a derivative of lithography technology.
Therefore, nano-imprint technology is also known as the core technology of future semiconductor manufacturing.
At present, many research institutions and manufacturers have increased their investment in nano-imprint. In addition to Canon, foreign manufacturers such as EV Group, Nanonex Corp, Obducat AB, SUSS MicroTec, and others have produced nano-imprint lithography equipment. There are also many domestic manufacturers accelerating their layout in the nano-imprint track, such as Qingdao Tianren Micro-Nano, Suzhou Soochow University Micro-Nano, Goer Shares, Suzhou Guangdu Micro-Nano, Sheng Yin Optoelectronics, Xin Du Wei Micro-Nano, Aimo Technology, and so on.
Tianren Micro-Nano, a domestic leading manufacturer favored by Huawei Harbin, currently has products covering complete equipment, molds, and imprinting materials. It has developed several high-precision ultraviolet nano-imprint equipment and has achieved mass production of high-precision (better than 10nm) and high aspect ratio (better than 10:1) nano-structure replication on a maximum 150/300mm substrate area.
The field where nano-imprint technology may be the first to land is perhaps the storage chip.
In the field of chip manufacturing, the most suitable for nano-imprint technology is the storage chip, especially 3D NAND, DRAM, and other storage chips. Looking at Canon's planned roadmap for nano-imprint equipment, the application of nano-imprint will start from 3D NAND storage chips, gradually transition to DRAM, and finally achieve the manufacturing of CPU and other logic chips.
Storage manufacturers are very strict in controlling costs in chip manufacturing, and the design margin can withstand certain defects without affecting the yield rate. Relaxing the requirements for defects, many storage manufacturers have already planned to use nano-imprint technology to manufacture storage chips.
Japanese storage manufacturers such as Kioxia and Toshiba have started to layout nano-imprint technology very early. In March of this year, Micron Technology announced plans to be the first to support Canon's nano-printing technology, thereby further reducing the single-layer cost of producing DRAM storage chips. Previously, the memory giant SK Hynix also introduced Canon's nano-imprint machine for 3D NAND production testing.
The combination of nano-imprint technology and storage chips will greatly improve the production efficiency of storage manufacturers and reduce costs. After the large-scale commercialization of nano-imprint equipment in the field of chip manufacturing, its advantages will be more obvious.Therefore, nanoimprint technology is also referred to as the most promising technique to replace existing lithography technology.
04
Choice Three: Electron Beam Lithography (EBL & MEBL) Technology
Speaking of electron beam lithography technology, it is necessary to mention the principle of lithography technology again here.
As we all know, lithography is the most technically challenging and also the most critical technical step in the entire micro-fabrication process. So-called lithography is to "etch" the required patterns on the surface of a thin layer of photoresist by controlling the beam of light. The chemical properties of the photoresist will change at the position where the light beam is illuminated. The exposed parts will be removed (positive photoresist) or retained (negative photoresist) after soaking in the developer solution.
The wavelength of the light source is the main reason affecting the lithography accuracy. Due to the limitation of the light source wavelength, X-ray exposure can achieve an accuracy of about 50nm, and the exposure accuracy of deep ultraviolet light sources is around 100nm. However, the wavelength of electrons is relatively small, so the processing accuracy of electron beam lithography can reach below 10nm.
Electron beam lithography has become one of the most concerned next-generation lithography technologies due to its high resolution, stable performance, and relatively low cost.
Electron beam lithography can be divided into two types according to the exposure method: projection exposure and direct writing exposure. Projection exposure projects the mask pattern onto the photoresist surface by controlling the electron beam to illuminate the mask pattern, transferring the pattern on the mask to the photoresist. The principle is similar to that of a camera, where the subject is like the mask, and the photoresist is like the film. The subject is projected onto the film through the illumination of light.
Direct writing lithography does not require a mask plate. It directly controls the electron beam spot to illuminate the photoresist surface along a preset trajectory through the magnetic field, completing the pattern transfer, just like drawing. The pencil is similar to the electron beam, the paper is similar to the photoresist, and our hand is similar to the magnetic field. By controlling the movement of the pencil with the hand, the drawing is completed.
Due to the traditional lithography technology based on masks, its cost is increasing exponentially. Maskless electron beam lithography technology provides a complementary option because it does not require expensive photomasks, and direct writing technology is very attractive. However, the throughput of single-beam electron beam lithography is too slow, and the cost is too high for batch IC production. Analysts also frankly stated that the real problem with direct writing is the throughput. Direct writing lithography technology, even with hundreds of thousands or even a million beams, is still too slow for wafer lithography.Therefore, single-beam direct writing tools can only be used for niche applications such as compound semiconductors and photonics.
To address the challenge of slow writing, Multibeam has provided its solution.
Recently, Multibeam, a major player in electron beam lithography technology, launched the MB Platform—a world-first multi-column electron beam lithography (MEBL: Multicolumn E-Beam Lithography). According to the introduction, its new lithography system is a system specifically designed for mass production. The fully automatic precision patterning technology will be used for rapid prototyping, advanced packaging, high-mix production, chip ID, compound semiconductors, and other applications. Multibeam stated that the platform just released by the company will completely change electron beam lithography with new productivity advantages, while achieving high resolution, fine features, wide field of view, and large depth of field.
Multibeam CEO and Chairman David K. Lam said in an interview that Multibeam can make the production efficiency of some parts of chip manufacturing 100 times higher than existing systems.
In Multibeam's view, this is a game-changing device. However, as early as the 1980s, it was widely believed that optical exposure had come to an end and electron beam lithography was the most promising alternative, but more than 30 years have passed, and electron beam lithography still cannot replace optical exposure. A complementary pattern has gradually formed in the development of the two lithography technologies.
With the rapid development of technology, the emergence of new lithography technologies undoubtedly injects new vitality into the industry. In the future, what surprises these innovative lithography technologies will bring to the semiconductor industry, we will wait and see!
Comments